A precise and effective temperature control system is extremely important in food processing. Temperature affects virtually all biological, physical, and chemical processes that occur during food processing and affect the product's final properties. A temperature control system gives the user an active role and enables them to regulate the processes taking place inside the tank and guide them in the desired direction. Choosing a suitable cooling and heating method also contributes to an energy-efficient and economical device operation.
The cooling/heating system should be selected based on:
- tank/device purpose of use (fermentation, maturation, storage)
- required temperature settings (min. and max. temperature, time frame for reaching the desired temperatures)
- predicted average ambient temperature where the tank/device will be installed
Plate heat exchanger
Plate heat exchangers are made of stainless steel EN 1.4301. Their smooth electropolished surface prevents the formation of deposits (e.g. tartrates). The cooling medium used is water or glycol.
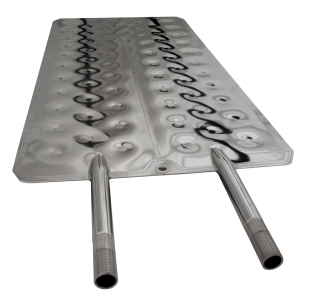
Double jacket (pillow plate)
A jacket with a heat exchanger consists of two sheets of metal, which are laser welded together.
Once the sheets are joined, the jacket is plastically deformed (inflated) with water pressure. This creates a special single embossed profile or pillow plate, through which the cooling/heating medium flows.
Tanks with a double jacket are ideal for use in the food industry and in other industries where processes can only be carried out under recommended temperature settings (winemaking, beer brewing, production of juices and dairy products etc.).
Technical characteristics
The surface of the double jacket can be ground, mechanically polished, circle polished, scotch brite, or sandblasted. The dimensions, surface finishing, and types of connections on the jacket are in accordance with the submitted specifications and customer requirements.
Double jacket pressure:
Test pressure | max. 6 bar |
Operating pressure | max. 3 bar |
Medium | water, glycol |
The pressure test is performed in accordance with the TÜV certificate for double jacket testing.
It is necessary to ensure a sufficient double jacket inlet/outlet pressure difference based on the cooling medium, the surface area of the double jacket, and the desired flow rate.
Types of double jackets
Laser welding provides greater flexibility when welding the double jacket. The laser technology enables different welding lines, which facilitates the adaptation to the existing elements on the base sheet (doors, connectors) and minimizes cooling/heating surface loss.
A double jacket can be welded onto:
- the base sheet (jacket) of a cylindrical, rectangular, or oval tank,
- a flat, conical, or torispherical bottom,
- a pneumatic press drum.
The suitable double jacket dimensions and design are determined based on:
- tank type (cylindrical, rectangular, oval, conical)
- tank dimensions (diameter, volume)
- desired position of the cooling/heating medium flow connectors
- recommended double jacket surface area, which will enable efficient cooling
Double jacket types and component connection
Cooling coil
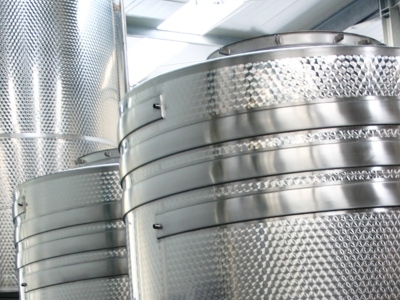
Technical characteristics
Test pressure | 3.6 bar |
Operating pressure | max. 2.5 bar |
Medium | water, glycol |
Base jacket thickness | min. 2.0 mm |
It is necessary to ensure a sufficient cooling coil inlet/outlet pressure difference based on the cooling medium, the length of the coil, and the desired flow rate.
How to ensure effective and efficient cooling?
In order to achieve effective and efficient cooling, it is important that the cooling coil cover a sufficiently large part of the tank surface and that we ensure a suitable medium flow rate inside the coil.
Things to take into account during planning:
- tank type and dimensions (volume, diameter)
- tank's purpose of use (storage, fermentation etc.)
- estimated average ambient temperature where the tank will be installed
- desired cooling temperature range
- desired product cooling intensity inside the tank
Double bottom with heaters
A double bottom is a special tank bottom design with a water compartment and electric heating element connectors. Water heating in the double bottom can be regulated manually with the heater thermostat, or automatically (heater ON/OFF) with the SPR8 temperature regulator.
Technical characteristics:
- suitable for tanks with flat bottom
- required number of heaters depends on tank volume; usually one heater per 3000 - 4000 L of tank volume
- the water in the double bottom is under atmospheric pressure; no overpressure is allowed inside the water compartment
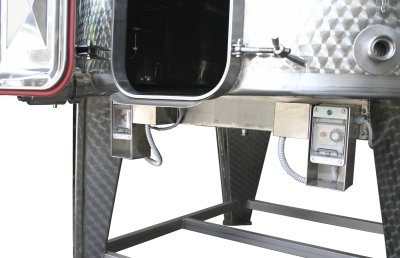
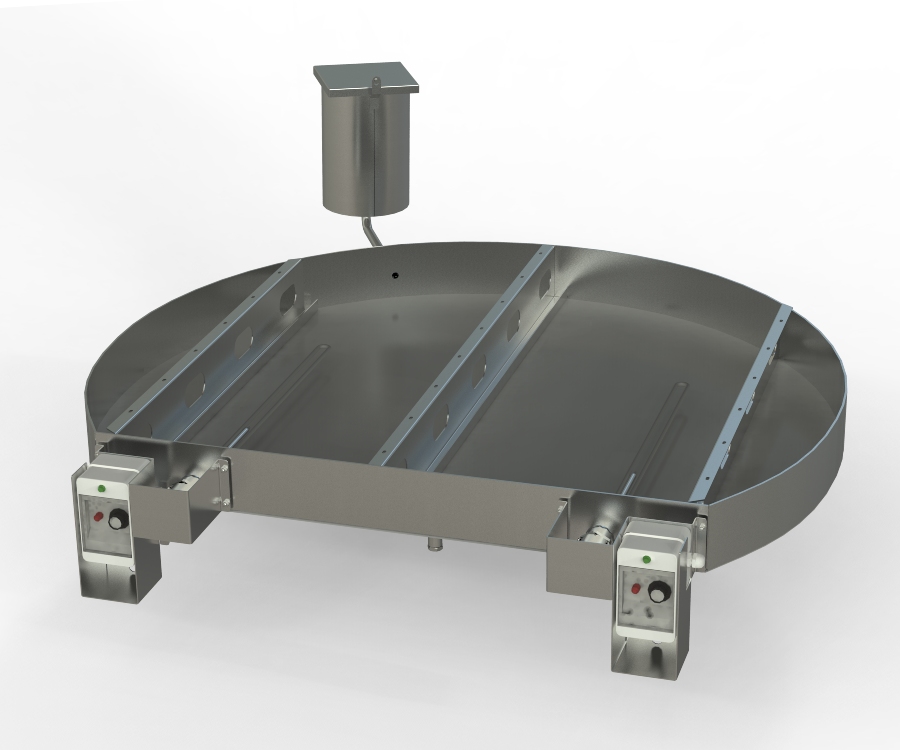