Today we are often faced with the dilemma of how to recognize true quality in a flooded market and find a product that will meet our expectations. Our requirements differ. Some people may prioritize high quality, others a favorable price or a pleasing design. Ideally, we are able to find a product that combines all these features - an aesthetic appeal and a good price-quality ratio.
While browsing the web and collecting offers from different manufacturers, it often turns out that the price range for products which are similar in appearance and manufactured for the same purpose of use can vary widely. This is also the case with tanks and other stainless steel products.
The Škrlj company has been manufacturing winemaking equipment for decades. In our experience, the final price of stainless steel wine tanks depends mainly on the materials used, the surface and weld finish, the tank components and accessories and also on some other details that may not be noticeable, but have a significant impact on product usability and durability.
In this article we offer some guidelines that can help you compare wine tanks made by different manufacturers.
1) Quality and traceability of the materials used
Check which materials were used to manufacture the tank. Does the manufacturer guarantee material traceability? Can they provide the suitable certificates for the materials used? A material certificate is a quality assurance document which certifies that the material has been processed in accordance with the requirements, and that its chemical properties ensure sufficient corrosion resistance.
2) Sheet metal thickness
Check the thickness of the sheet metal, used by the manufacturer to make the tank jacket, bottom, and lid. The difference in sheet thickness is practically imperceptible. At least with a new product. If a tank is made of thinner sheet metal, it is more sensitive to impacts and more prone to deformation, especially where the doors and welded connections are located.
3) Welding process
Which welding process does the manufacturer use to weld the tank components (jacket, lid, bottom, connections) and the tank's double jacket? Which technique is used to weld the pipes and pipe fittings? Modern, automated welding processes enable uniform and solid welds, without the errors that often occur during manual welding.
4) Surface and weld finish
Check the standard surface and weld finishes, offered by the manufacturer. Smooth internal tank surfaces and welds enable simple cleaning and facilitate hygiene maintenance.
The external surface of our wine tanks is most often circle polished (flowered finish). If a surface is circle polished, mechanical damage is less noticeable and maintenance is easy. An external surface with a ground or Scotch Brite finish, which are also common for wine tanks, gives the product a more modern and sophisticated appearance. However, the maintenance of ground surfaces is more demanding. Scratches and other defects are quickly noticeable on ground surfaces and are much more difficult to repair than on surfaces with a flowered finish.
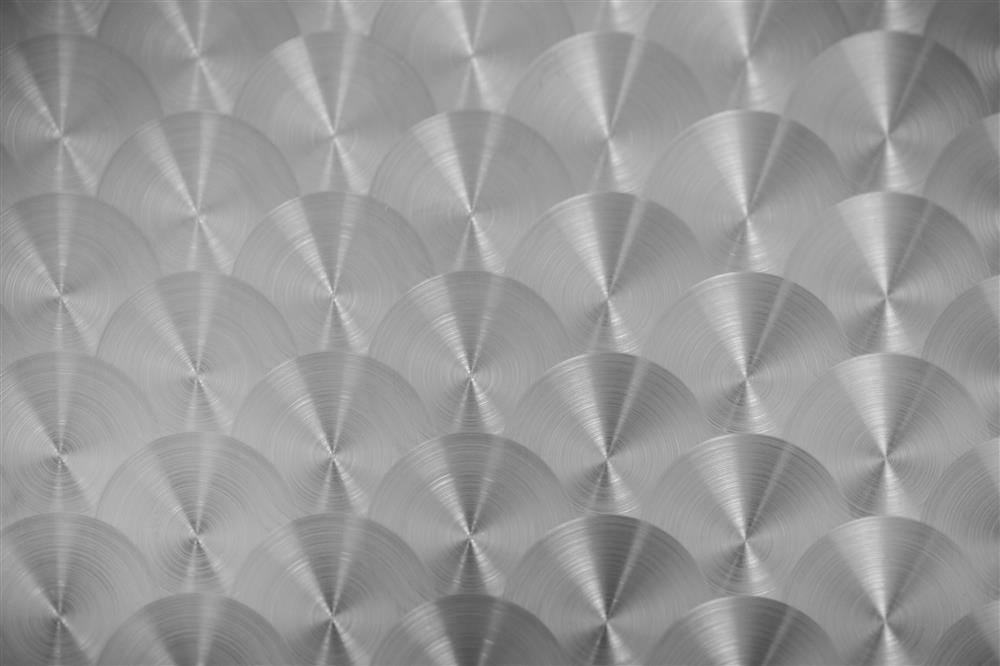
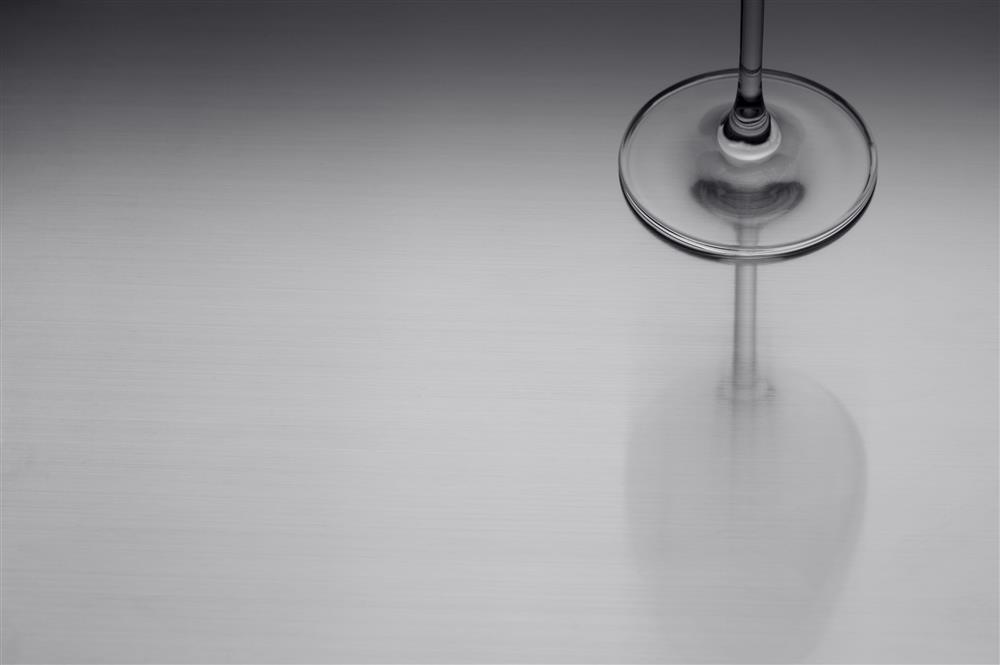
5) Tank equipment
Check which equipment is already included in the basic tank price and what you would have to order additionally.
6) References
Check the manufacturer's reference list.
Best practices for great results
Thanks to our 50 years of experience in manufacturing stainless steel equipment, we have gained extensive knowledge on stainless steel.
Our company has a modern production facility with a high degree of automation and robotization of the work processes. The production program includes stainless steel tanks and devices for various industries, especially for winemaking, beer brewing, pharmacy, and the food industry.
Everything in one place - our own design, planning, and production
The entire work process, from planning to production, is carried out in one location - on the premises of the Škrlj company. This enables product traceability throughout the entire production process which consequently reduces the risk of product damage that can occur during transport between different locations.
We believe our experience in different advanced industrial fields (pharmaceuticals) is also a great advantage - the skills we've developed and the technologies we use for those products enable us to manufacture wine tanks of exceptional quality.
Standard tanks and custom designs
Our wide range of standard tanks is available on our website.
Some winegrowing regions differ greatly in terms of grape processing technology and tradition, which we took into account when preparing our selection of standard tanks. In addition to the basic version (UN), we also offer tanks for the Austrian (AT), German (DE), French (FR), and American (US) markets.
If a tank's standard equipment does not meet your requirements, you can access the optional and additional equipment in the tank's detailed description and assemble the tank according to your wishes. We also manufacture tanks with other volumes, dimensions, and equipment.
Elaborate projects
We also have a lot of experience with larger and more elaborate projects that, in addition to the production of tanks, also require us to prepare a layout, which often includes tanks in combination with platforms, walkways, staircases, and other equipment.
Tank, platform, walkway, and equipment placement
Certified materials and equipment. Product traceability.
We guarantee material and equipment traceability. We can provide suitable certificates for the materials used.
The thickness of the sheet metal that will be used to manufacture tanks is clearly indicated in our offers. The customer knows what he'll get.
Modern production processes
The sheet metal is cut with a laser. The edges of a laser-cut material are smooth, uniform and do not require further processing.
Modern laser technology is also our standard for double jacket welding.
In laser welding, the heat input is limited and strictly controlled (time, position), so there is no deformation of the base material. Adapting to the elements on the basic tank jacket (door, connectors) is simple, which means cooling surface loss is minimal.
A laser-welded cooling jacket is unobtrusive, sometimes it even appears decorative.
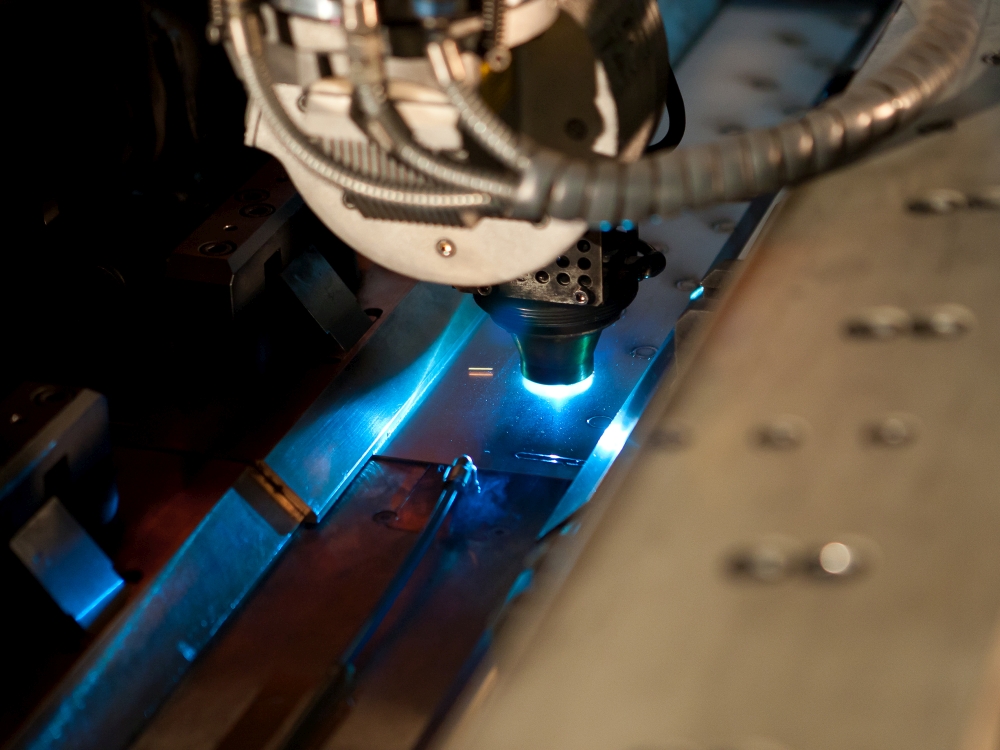
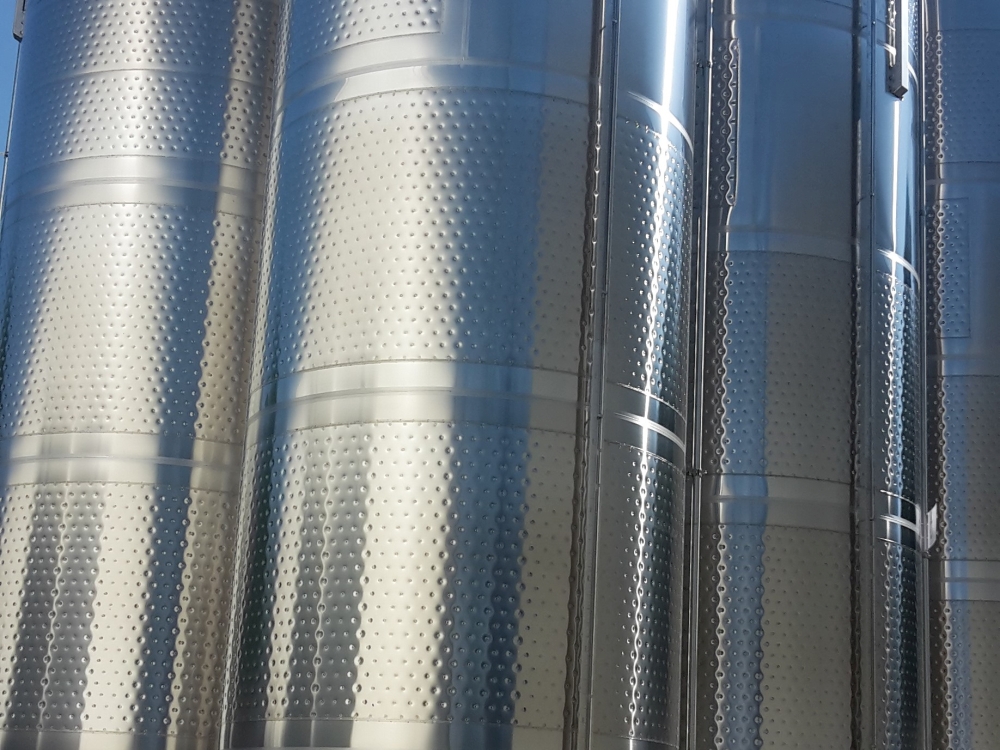
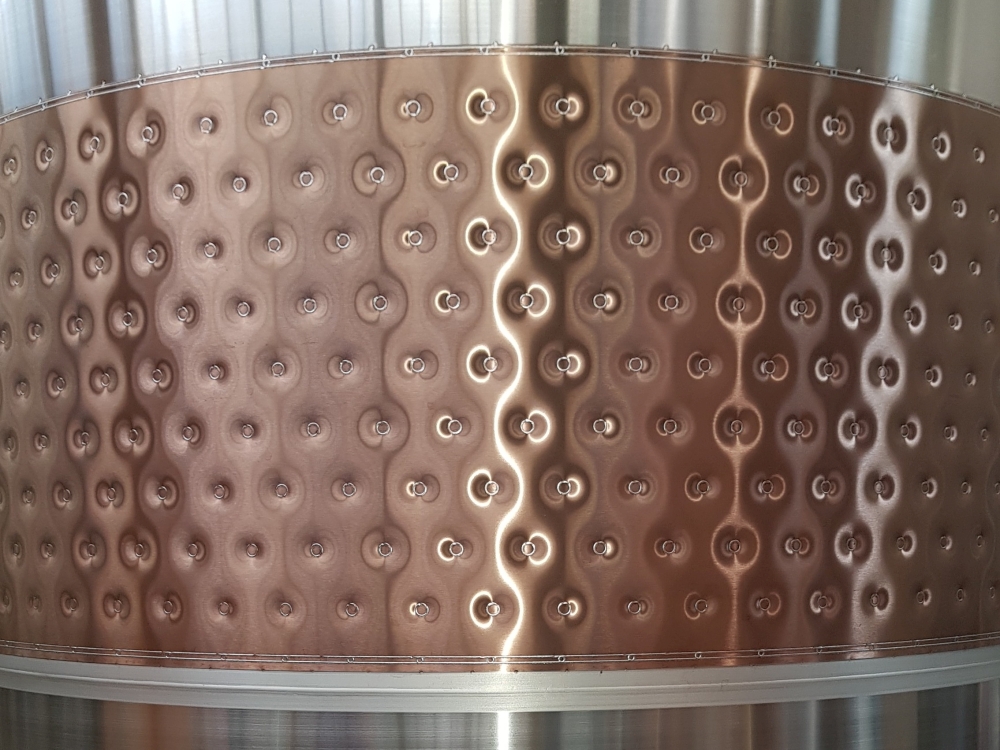
... and some more technical advantages of Škrlj tanks:
- hygienic tank leg design: The legs are completely closed, without sharp edges, and welded to the bottom of the tank along their entire perimeter. Simple maintenance and cleaning.
- orbital pipe welding: Orbital welding is an automated welding process of joining two pipes by creating a butt weld. The resulting high-quality weld is smooth and has no dents or bumps where impurities could accumulate. This technology is mostly used in industries that require precise and flawless welds (pharmaceutical, chemical, and food industries). In the Škrlj company, we also orbitally weld some connectors on wine tanks (e.g. the filling connector on the tank top).
Online access to offers, orders, and documentation
Our customers can easily access their offers, orders, and product documentation through our website. This way they can track their offers and orders and see their status.
Customer support
At Škrlj, we are aware that a successful production process depends on many factors: precise planning, production factors, the suitability of the equipment we receive from our suppliers, and the smooth flow of information between the customer, the distributor/sales representative, and the manufacturer.
Some problems may arise along the way that cannot be predicted in advance. In such circumstances, we always do our best to resolve the problem; we offer remote customer support and if the problem cannot be resolved remotely, we send our service technicians to figure it out.